SunFarmer
New Member
Hello Forum,
I’m working on the low voltage, high current DC portion of my system. I’ve settled on the layout shown in the diagram, at least for now (hoping to at least partially commission the system so I can claim the USA tax credit for this year).
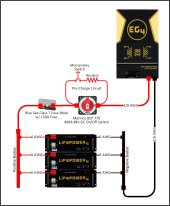
Initially, I was going to use a large DC circuit breaker between the battery bank and inverter. But then I read about resistance, voltage drop and fire caused by reversed polarity, so I decided to stay away from DC breakers. Then I saw David Poz’s excellent review of the Nader 125A breaker, my hope went up that it could be a good fit for me, until the end of David’s video where he had to take the current way above 125A for ten minutes before the breaker tripped. And the breaker got very hot in the process. Here gain I decided to avoid large DC breakers.
So, I chose to use a switch and a fuse, although I’m still not 100% sure about it. The best switch I could fine is only rated for 48V DC, whereas I wish it were rated for 60V. For over current protection I chose a 150A class-T fuse, which is just hair under my calculated minimum fuse size. I then realized that fuses, like breakers, can go way above their rated current before popping. What’s a DIYer to do?
Esteemed forum members, please provide your option on the best way to protect inverters, batteries and wiring from short circuits or other faults?
Thank You
I’m working on the low voltage, high current DC portion of my system. I’ve settled on the layout shown in the diagram, at least for now (hoping to at least partially commission the system so I can claim the USA tax credit for this year).
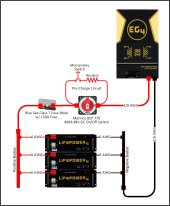
Initially, I was going to use a large DC circuit breaker between the battery bank and inverter. But then I read about resistance, voltage drop and fire caused by reversed polarity, so I decided to stay away from DC breakers. Then I saw David Poz’s excellent review of the Nader 125A breaker, my hope went up that it could be a good fit for me, until the end of David’s video where he had to take the current way above 125A for ten minutes before the breaker tripped. And the breaker got very hot in the process. Here gain I decided to avoid large DC breakers.
So, I chose to use a switch and a fuse, although I’m still not 100% sure about it. The best switch I could fine is only rated for 48V DC, whereas I wish it were rated for 60V. For over current protection I chose a 150A class-T fuse, which is just hair under my calculated minimum fuse size. I then realized that fuses, like breakers, can go way above their rated current before popping. What’s a DIYer to do?
Esteemed forum members, please provide your option on the best way to protect inverters, batteries and wiring from short circuits or other faults?
Thank You