for my 12 volt solar system I am replacing 4- 6v trojan L16 batteries with 6 -12v AGM's (power tech BAT-8A8D). I have been told that hooking all the batteries in parallel will cause the first battery in the chain connected to the inverter to take most of the wear so Rather than run them all in parallel ganged together i am thinking to connect them to a pos and neg bus bar and then hook the charge controller and inverter to the bus bar.
so my questions are:
-is this the best solution to join the batteries? if not, suggestions?
what size cable should i use to connect from each battery to the bus bar?
where is the best place to purchase the bus bars?
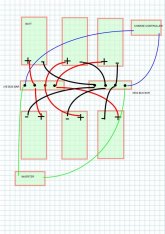
so my questions are:
-is this the best solution to join the batteries? if not, suggestions?
what size cable should i use to connect from each battery to the bus bar?
where is the best place to purchase the bus bars?
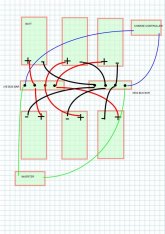