You guys are driving me crazy! Staubli. that is the company that now owns/manufactures what was the original MC4 connector and tools to crimp, tighten and take apart.
www.staubli.com
If you want to purchase originals and spend more, then by all means.
THERE IS NO STANDARD FOR KNOCKOFFS OF MC4 CONNECTORS. JUST COPIES. SOME ARE BETTER THAN OTHERS.
PROCEDURE:
Buy a pair of MC4 tools. In every case, they are heavy plastic and are used to take the connectors apart and to screw the wire connector tight to the body of the MC4 and unscrew them.
Buy MC4 connectors. Buy the original Staubli or a very good knockoff. Some knockoffs are so cheaply made that they have poor O-rings for waterproof seals, and very thin metal connectors as well as being out of physical spec by enough of a size that they only fit themselves together.
Purchase an MC4 crimping tool. You need a specific tool to crimp PV wire to the MC4 metal conductor pins.
I already posted above recommended tools. I have removed and made hundreds of MC4 connections using Staubli and good knockoffs.
You don't need zip ties or other fancy stuff. You need to be able to cut and strip PV wire 12 awg and 10 awg.
Innovative solutions for higher productivity
Stäubli provides mechatronic solutions in its four Divisions Electrical Connectors, Fluid Connectors, Robotics and Textile machinery.
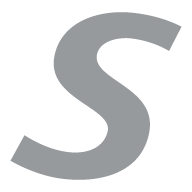
If you want to purchase originals and spend more, then by all means.
THERE IS NO STANDARD FOR KNOCKOFFS OF MC4 CONNECTORS. JUST COPIES. SOME ARE BETTER THAN OTHERS.
PROCEDURE:
Buy a pair of MC4 tools. In every case, they are heavy plastic and are used to take the connectors apart and to screw the wire connector tight to the body of the MC4 and unscrew them.
Buy MC4 connectors. Buy the original Staubli or a very good knockoff. Some knockoffs are so cheaply made that they have poor O-rings for waterproof seals, and very thin metal connectors as well as being out of physical spec by enough of a size that they only fit themselves together.
Purchase an MC4 crimping tool. You need a specific tool to crimp PV wire to the MC4 metal conductor pins.
I already posted above recommended tools. I have removed and made hundreds of MC4 connections using Staubli and good knockoffs.
You don't need zip ties or other fancy stuff. You need to be able to cut and strip PV wire 12 awg and 10 awg.