Hi Folks
I have some questions regarding M8 and M10 lugs and I'd be grateful for some help.
My 12V DIY solar system consists of 5 SCCs (200A total max), 2 Battery Chargers (120A total max), 2 LifePo4 batteries, a BMV-712 shunt, 2 x Victron 250A 6 post Bus Bars (+ve and -ve), and a Giandel 4000W inverter. All in parallel via the bus bars (with the exception of the batteries, which are joined in parallel directly together).
1) My equipment, annoyingly, has different sized terminal posts/holes from each other. In principal, is it safe to use an M10 lug on an M8 stud/hole (using 8mm nuts/screws), as long as the surface area around the M10 lug is in contact with the metal plate surrounding the post/hole?
2) Is it safe and accepted practice to have multiple lugs on a single post/hole?
3) As mentioned above, I use Victron 250Amp busbars. Whilst 250Amps is enough for the total current from my SCCs and battery chargers (which are never on at the same time at max current), the current from the batteries to the inverter could be as high as 500Amps. Am I still ok to use these undersized busbars as long as my inverter lugs and battery lugs are on the same post (thus, in theory, no current from the battery is going through the bus bar) ?
4) If safe, what is the best way to mount 2 eg. M10 lugs together on the same post/hole? I can never seem to get 100% coverage of the upper lug on the bottom one.
This is what I have (ignore cable colours!):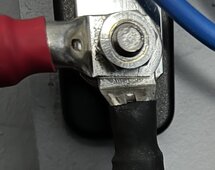
5) Does anyone use a Littlefuse Mega with M10 lugs? If so, is this safe?
6) What is the tradeoff of doing 1-3 above vs just reordering cables with correct lugs as well as the Victron 600A busbars (apart from cost, of course). I'd rather not have to do this as long as 1-3 is safe, but your help would be appreciated.
Thanks folks!
Cheers
JT
I have some questions regarding M8 and M10 lugs and I'd be grateful for some help.
My 12V DIY solar system consists of 5 SCCs (200A total max), 2 Battery Chargers (120A total max), 2 LifePo4 batteries, a BMV-712 shunt, 2 x Victron 250A 6 post Bus Bars (+ve and -ve), and a Giandel 4000W inverter. All in parallel via the bus bars (with the exception of the batteries, which are joined in parallel directly together).
1) My equipment, annoyingly, has different sized terminal posts/holes from each other. In principal, is it safe to use an M10 lug on an M8 stud/hole (using 8mm nuts/screws), as long as the surface area around the M10 lug is in contact with the metal plate surrounding the post/hole?
2) Is it safe and accepted practice to have multiple lugs on a single post/hole?
3) As mentioned above, I use Victron 250Amp busbars. Whilst 250Amps is enough for the total current from my SCCs and battery chargers (which are never on at the same time at max current), the current from the batteries to the inverter could be as high as 500Amps. Am I still ok to use these undersized busbars as long as my inverter lugs and battery lugs are on the same post (thus, in theory, no current from the battery is going through the bus bar) ?
4) If safe, what is the best way to mount 2 eg. M10 lugs together on the same post/hole? I can never seem to get 100% coverage of the upper lug on the bottom one.
This is what I have (ignore cable colours!):
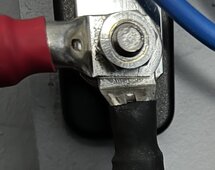
5) Does anyone use a Littlefuse Mega with M10 lugs? If so, is this safe?
6) What is the tradeoff of doing 1-3 above vs just reordering cables with correct lugs as well as the Victron 600A busbars (apart from cost, of course). I'd rather not have to do this as long as 1-3 is safe, but your help would be appreciated.
Thanks folks!
Cheers
JT
Last edited: