totalconfusion
New Member
- Joined
- Dec 24, 2020
- Messages
- 62
Hello, I have some questions about a build I’m working on. It’s mostly Victron equipment and I wanted to make sure everything is communicating the way it should be, I also have some questions regarding isolators, fuses and cable sizing.
Victron SmartSolar MPPT 250/100
Victron MultiPlus-II 48/5000/70-50
Victron Smart BatteryProtect 48V-100A
Victron Lynx Distributor (Power distribution board)
Victron BMV-712 Smart Shunt (500A)
x2 PylonTech US5000B 48V 100AH LiFePO4 batteries
PylonTech cables = 4x 2M Power Cables (4AWG, Peak Current Capacity 120A, 100A constant)
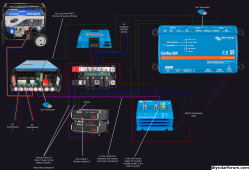
// Batteries
1. Where do I define the max discharge limit in software? Is this part of the PylonTech BMS and can I change it using the Cerbo or do I have to interface with the BMS itself? I would like to hard limit it to 160A (0.8C on each battery)
2. The batteries have a max discharge current of 100A each but should be run at 80A or below. When run in parallel this discharge current will be 200A-160A. Is this correct?
3. I have set up DVCC. As far as I know, it’s just a way for the BMS to control the MPPT output into the batteries, is this correct? What are the advantages of using the PylonTech batteries BMS to control the MPPT as opposed to entering the charge parameters into the MPPT manually? Do they have inbuilt temperature sensors that guide the charging profile or something?
4. Is the cable configuration on the batteries correct? Should they be paralleled using the PylonTech parallel cable or is this a weak point that is under rated for the current going through it? Would I be better off ditching the short parallel cables and running both batteries independently to the Lynx distributor?
5. Should the PylonTech batteries be part of the same CAN network as the Inverter and MPPT or are the batteries better directly connected to the Cerbo by a separate VE CAN to CAN-Bus RJ45?
// Fusing and isolation
1. Should I be using x4 Class T fuses on all the battery outputs?
2. Regarding battery isolators. Are they just another point of failure and a waste of money considering the batteries themselves have a circuit breaker? If they are required, should I use them after the Class T fuses and combine the two positives and two negatives to x2 isolators, or do I need x4 isolators?
3. Post BatteryProtect I intend to have a fused 48VDC distribution board. Should I stick with MEGA fuses here like I have in the Lynx distributor? The BatteryProtect is only good for 100A so should I put a 100A fuse between the BatteryProtect and 48VDC distribution board? Or does the BatteryProtect have it’s own fuse and/or current limiting?
4. Should I fuse the MPPT battery positive and negative cables to the Lynx Distributor even though it’s a source and not a load? I guess it would protect everything else attached to the Distributor in the event the MPPT epicly fails. Should this 48VDC fuse be in the range of 120A-140A? Does the PV max current on the MPPT PV input come into play here at all for calculating the fuse value of the MPPT output? The PV input is coming in at 50A max.
I got the 120A-140A value from section 4.2 of the MPPT manual
https://www.victronenergy.com/uploa...-MPPT_solar_charger_manual-pdf-en.pdf#page=15
5. Fuse size for DC inverter input = 200A (9000 / 48 = 187.5A) - Is this calculation correct or is it undersized for peak loads?
Inverter manual: https://www.victronenergy.com/upload/documents/Datasheet-MultiPlus-II-inverter-charger-EN.pdf
// Cable sizing
1. Do the PylonTech battery cables have to take the collective loads of MPPT charging, inverter charging and battery discharge at the same time or will it be split between the four cables? If I were to turn the circuit breaker on one of the batteries off, would that overload the second battery's cables in a max current situation?
Battery max discharge = 160A-200A
Inverter max charge = 70A
MPPT max charge = 100A
Total = 330A-370A
2. Does lug positioning on the bus bar matter? Should I put the MPPT lug closest to the battery IN on the Lynx distributor?
// Communications
1. Is the Cerbo itself running VenusOS?
2. What is the ‘Battery Monitor’ setting? Should I set this as the PylonTech BMS?
3. Can I connect a VenusOS RasPi directly to the Cerbo Wi-Fi network or is it only for setup and I’ll need a real network that the Cerbo connects to?
3. What does the HDMI output of the Cerbo do? Can I hook this up to another 7” screen for a second display next to the Cerbo? Does the Cerbo accept touch input over USB?
4. Where can I confirm how the devices are communicating? I want to run everything off a daisy chained CAN. I want to confirm some devices aren’t using Bluetooth or VE.Direct for example.
5. Do I have to manually activate ‘Power control’ and ‘PowerAssist’ in software or is it enabled by default?
// Miscellaneous
1. For the 48VDC distribution side of things I’m thinking of getting one of these:
www.bluesea.com
Are there any good quality 48V capable fused distribution boards that have both positive and negative bus bars integrated into the one unit other than the Victron Lynx Distributor? I had a look at BlueSea and couldn’t find one. Extra points if it has M8 studs
2. I’ve really struggled trying to get voltage ranges and charging parameters for the PylonTech batteries. The best I could get from the battery datasheet is:
Depth of discharge 95%
DischargeVoltage (VDC) 43.5~53.5
ChargeVoltage (VDC) 52.5~53.5
RecommendedCharge/Discharge Current - 80A
Max Continuous Charge/Discharge Current - 100A
How can I use this information to set some reasonable values for low voltage disconnects in both the BatteryProtect and MultiPlus-II Inverter?
What kind of DoD should I use? 90-95%?
Should I set the Inverter LVD to kick in at a slightly higher voltage than the BatteryProtect remote LVD tells it to turn off?
What bulk, absorption and float values can I use with these batteries?
3. With the BatteryProtect, should I be using mode B (relay mode)? Also how does the remote on/off for the inverter work, does it just short the wire or send a pulse?
4. Is it possible to configure AC OUT 2 on the MultiPlus II Inverter so it acts like AC 1 OUT? As in it’s always on and not contingent on there being AC incoming ie: from a generator.
5. Where can I set generator remote start parameters? I want the genset to kick in when the batteries get below 50% and keep going until they are fully charged. That way the generator won’t be stopping and starting all the time. Is this a good idea? Should I set the genset to only charge to 90% of capacity?
6. The BMV smart shunt and Cerbo have temperature sensing. Should I buy a temperature probe or would the temperature sensing do nothing on the Lynx distributor? They have weird SurLok connectors on the PylonTech batteries, not standard studs so I can’t see a way to get it on the battery terminals.
Thanks heaps
Victron SmartSolar MPPT 250/100
Victron MultiPlus-II 48/5000/70-50
Victron Smart BatteryProtect 48V-100A
Victron Lynx Distributor (Power distribution board)
Victron BMV-712 Smart Shunt (500A)
x2 PylonTech US5000B 48V 100AH LiFePO4 batteries
PylonTech cables = 4x 2M Power Cables (4AWG, Peak Current Capacity 120A, 100A constant)
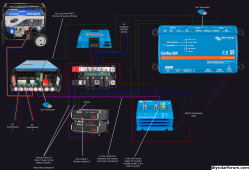
// Batteries
1. Where do I define the max discharge limit in software? Is this part of the PylonTech BMS and can I change it using the Cerbo or do I have to interface with the BMS itself? I would like to hard limit it to 160A (0.8C on each battery)
2. The batteries have a max discharge current of 100A each but should be run at 80A or below. When run in parallel this discharge current will be 200A-160A. Is this correct?
3. I have set up DVCC. As far as I know, it’s just a way for the BMS to control the MPPT output into the batteries, is this correct? What are the advantages of using the PylonTech batteries BMS to control the MPPT as opposed to entering the charge parameters into the MPPT manually? Do they have inbuilt temperature sensors that guide the charging profile or something?
4. Is the cable configuration on the batteries correct? Should they be paralleled using the PylonTech parallel cable or is this a weak point that is under rated for the current going through it? Would I be better off ditching the short parallel cables and running both batteries independently to the Lynx distributor?
5. Should the PylonTech batteries be part of the same CAN network as the Inverter and MPPT or are the batteries better directly connected to the Cerbo by a separate VE CAN to CAN-Bus RJ45?
// Fusing and isolation
1. Should I be using x4 Class T fuses on all the battery outputs?
2. Regarding battery isolators. Are they just another point of failure and a waste of money considering the batteries themselves have a circuit breaker? If they are required, should I use them after the Class T fuses and combine the two positives and two negatives to x2 isolators, or do I need x4 isolators?
3. Post BatteryProtect I intend to have a fused 48VDC distribution board. Should I stick with MEGA fuses here like I have in the Lynx distributor? The BatteryProtect is only good for 100A so should I put a 100A fuse between the BatteryProtect and 48VDC distribution board? Or does the BatteryProtect have it’s own fuse and/or current limiting?
4. Should I fuse the MPPT battery positive and negative cables to the Lynx Distributor even though it’s a source and not a load? I guess it would protect everything else attached to the Distributor in the event the MPPT epicly fails. Should this 48VDC fuse be in the range of 120A-140A? Does the PV max current on the MPPT PV input come into play here at all for calculating the fuse value of the MPPT output? The PV input is coming in at 50A max.
I got the 120A-140A value from section 4.2 of the MPPT manual
https://www.victronenergy.com/uploa...-MPPT_solar_charger_manual-pdf-en.pdf#page=15
5. Fuse size for DC inverter input = 200A (9000 / 48 = 187.5A) - Is this calculation correct or is it undersized for peak loads?
Inverter manual: https://www.victronenergy.com/upload/documents/Datasheet-MultiPlus-II-inverter-charger-EN.pdf
// Cable sizing
1. Do the PylonTech battery cables have to take the collective loads of MPPT charging, inverter charging and battery discharge at the same time or will it be split between the four cables? If I were to turn the circuit breaker on one of the batteries off, would that overload the second battery's cables in a max current situation?
Battery max discharge = 160A-200A
Inverter max charge = 70A
MPPT max charge = 100A
Total = 330A-370A
2. Does lug positioning on the bus bar matter? Should I put the MPPT lug closest to the battery IN on the Lynx distributor?
// Communications
1. Is the Cerbo itself running VenusOS?
2. What is the ‘Battery Monitor’ setting? Should I set this as the PylonTech BMS?
3. Can I connect a VenusOS RasPi directly to the Cerbo Wi-Fi network or is it only for setup and I’ll need a real network that the Cerbo connects to?
3. What does the HDMI output of the Cerbo do? Can I hook this up to another 7” screen for a second display next to the Cerbo? Does the Cerbo accept touch input over USB?
4. Where can I confirm how the devices are communicating? I want to run everything off a daisy chained CAN. I want to confirm some devices aren’t using Bluetooth or VE.Direct for example.
5. Do I have to manually activate ‘Power control’ and ‘PowerAssist’ in software or is it enabled by default?
// Miscellaneous
1. For the 48VDC distribution side of things I’m thinking of getting one of these:
MRBF Surface Mount Fuse Block - Common Source - Blue Sea Systems
Easily and economically satisfies ABYC 7 circuit protection rule by mounting on a 3/8 battery post, battery switch or bus bar.

Are there any good quality 48V capable fused distribution boards that have both positive and negative bus bars integrated into the one unit other than the Victron Lynx Distributor? I had a look at BlueSea and couldn’t find one. Extra points if it has M8 studs
2. I’ve really struggled trying to get voltage ranges and charging parameters for the PylonTech batteries. The best I could get from the battery datasheet is:
Depth of discharge 95%
DischargeVoltage (VDC) 43.5~53.5
ChargeVoltage (VDC) 52.5~53.5
RecommendedCharge/Discharge Current - 80A
Max Continuous Charge/Discharge Current - 100A
How can I use this information to set some reasonable values for low voltage disconnects in both the BatteryProtect and MultiPlus-II Inverter?
What kind of DoD should I use? 90-95%?
Should I set the Inverter LVD to kick in at a slightly higher voltage than the BatteryProtect remote LVD tells it to turn off?
What bulk, absorption and float values can I use with these batteries?
3. With the BatteryProtect, should I be using mode B (relay mode)? Also how does the remote on/off for the inverter work, does it just short the wire or send a pulse?
4. Is it possible to configure AC OUT 2 on the MultiPlus II Inverter so it acts like AC 1 OUT? As in it’s always on and not contingent on there being AC incoming ie: from a generator.
5. Where can I set generator remote start parameters? I want the genset to kick in when the batteries get below 50% and keep going until they are fully charged. That way the generator won’t be stopping and starting all the time. Is this a good idea? Should I set the genset to only charge to 90% of capacity?
6. The BMV smart shunt and Cerbo have temperature sensing. Should I buy a temperature probe or would the temperature sensing do nothing on the Lynx distributor? They have weird SurLok connectors on the PylonTech batteries, not standard studs so I can’t see a way to get it on the battery terminals.
Thanks heaps
Last edited: