I have fun "fixing" and rebuilding things that don't really have much of a purpose. Just kind of gives me something to do, and gives a second life to an otherwise trash product. My most recent endeavor was soldering a bicycle tire valve onto the bottom of one of those air duster cans, you can fill it up with an air compressor to about 120 psi. It doesn't hold nearly as much air as the one you buy from the store, but for quick "psstss" to remove metal shavings or whatnot it works great, plus it's free to refill.
this is the photo of the one that worked super easily on my first try.
This one holds tight as can be, I drilled the hole, tapped it, threaded it, and added a little bit of solder. It worked on my first try, and couldn't have been easier, especially considering that the metal on the bottom of that can is paper thin.
My next project was to try to refill a dead fire extinguisher. Once all of the powdered stuff is gone, you can fill it about 3/4 with water use an air compressor to force air down the hose nozzle, and you get a mildly powerful water-based fire extinguisher, that's great for around a campfire or shop. My thought was to make it a lot easier to fill by adding an air valve to the side of the tank, I could also refill it with powder that way. The metal is about three times as thick, and I believe it to be aluminum. I drilled cleaned it down to bare metal, fluxed it, tapped it, and because it was thicker, I tried to use some Teflon tape to seal the threads up, but I was still getting a slow leak. I pulled it all apart, put it back together, and decided to try to solder the threads instead, this is my third try and I'm still getting a leak. I'm pretty experienced with solder, and I've tried it with two different kinds (leaded electrical solder, and non-leaded pipe solder), and it's still leaks. I've got it down to the point where it's a single bubble every couple minutes, but the joint just will not hold no matter what I do. I've screwed it in and unscrewed it so much at this point that the threads are somewhat loose, so that's a problem now too. Does anybody have any suggestions for how to make this work? I know this isn't a plumbing forum, but this is the forum that I'm a part of that is closest to an issue like this. Here's a photo of the one that just is not holding. Underneath of the solder ring is very clean bright fluxed aluminum, it's hard to see, but it's there, I'm not soldering directly to the paint. The solder just won't stick to the can no matter how clean or sanded it is. This one dropped from 100 psi to 90 PSI overnight, so it's not too far. I am also pulling the valve stems before I solder so they don't melt.
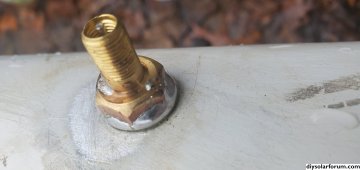
Any suggestions could be greatly appreciated.
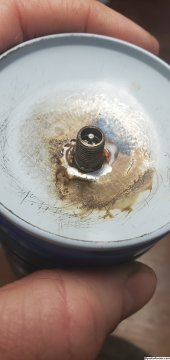
This one holds tight as can be, I drilled the hole, tapped it, threaded it, and added a little bit of solder. It worked on my first try, and couldn't have been easier, especially considering that the metal on the bottom of that can is paper thin.
My next project was to try to refill a dead fire extinguisher. Once all of the powdered stuff is gone, you can fill it about 3/4 with water use an air compressor to force air down the hose nozzle, and you get a mildly powerful water-based fire extinguisher, that's great for around a campfire or shop. My thought was to make it a lot easier to fill by adding an air valve to the side of the tank, I could also refill it with powder that way. The metal is about three times as thick, and I believe it to be aluminum. I drilled cleaned it down to bare metal, fluxed it, tapped it, and because it was thicker, I tried to use some Teflon tape to seal the threads up, but I was still getting a slow leak. I pulled it all apart, put it back together, and decided to try to solder the threads instead, this is my third try and I'm still getting a leak. I'm pretty experienced with solder, and I've tried it with two different kinds (leaded electrical solder, and non-leaded pipe solder), and it's still leaks. I've got it down to the point where it's a single bubble every couple minutes, but the joint just will not hold no matter what I do. I've screwed it in and unscrewed it so much at this point that the threads are somewhat loose, so that's a problem now too. Does anybody have any suggestions for how to make this work? I know this isn't a plumbing forum, but this is the forum that I'm a part of that is closest to an issue like this. Here's a photo of the one that just is not holding. Underneath of the solder ring is very clean bright fluxed aluminum, it's hard to see, but it's there, I'm not soldering directly to the paint. The solder just won't stick to the can no matter how clean or sanded it is. This one dropped from 100 psi to 90 PSI overnight, so it's not too far. I am also pulling the valve stems before I solder so they don't melt.
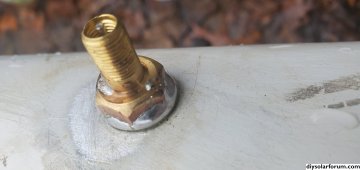
Any suggestions could be greatly appreciated.