A little update and some questions!
1. Got out to the cabin, and everything worked fine. The battery shut down due to low voltage in mid November, not odd, the sun doesn’t go over the horizon for my panels by then. Think we could have had snow too.
Last year, the batteries had emptied. When I got it going again, a cable burned up between the Smart Shunt and an Rasberry. During the spring, the MPPT wouldn’t load the batteries.
The only cable that potentially could circumvent the JK and empty the battery was the communication cable from the JK to a raspberry PI. If this cable could send electricity from the battery to the raspberry, it could explain why the cable between the raspberry and the SmartShunt burned up.
After I removed the communication cable from my JK to the Raspberry, everything started to work again and as mentioned, the batteries had not emptied.
I would think twice about hooking up a JK BMS with a communication cable (RS485 or whatever it is called) if the battery might run low!
Don’t know if anyone else had problems with it this?
2. When I started loading my battery, the settings of the JK was all over the place!! -20 UVP?? Calibrating current — 27A? I can’t speak, I am so shocked. ?
What is this?
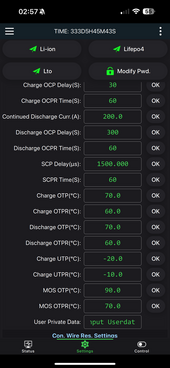