Ok, I've successfully implemented 3 of these PWM temperature controllers between the three existing fans.
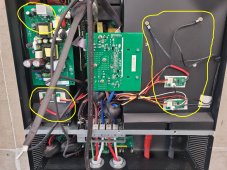
On the right side I've installed two of these PWM controllers for the two inverter unit fans and connected their temperature probes to the two heat sinks (existing holes can be used to screw them on) underneath these black plastic cover/air-channel.
On the left side I've installed the PWM controller for the MPPT fan. To attach the temperature probe to the MPPT heat sink, the PCB on the left side has to be lifted to get access to the MPPT heat sink (remove five screws, but nothing needs to be disconnected). The black plastic cover/air-channel under the PCB can be moved down while temporary remove a plastic plug to access the MPPT heat sink. There is an existing temperature sensor on the MPPT heat sink which could be used also to attach (screw) the additional temperature probe.
The pinout for the three fan connectors (Jst Xh 2.54 4 Pin Connector Male) is unusual. If you look from the top to the inverter PCB, the pinout from left to right is:
blue: PWM
red: +12V
white: sens/tacho
black: GND
So it's important to assign the correct pins to the PWM temperature modules because it's output is more like standard order (GND, +12V, sens, PWD). I made matching custom cables. The PWM pin on the inverter PCB fan connector is now not longer used (blue not longer connected) because the new temperature PWM controller now controls the fan speed. But the "trick" the inverter that the fan is really running, the sense/tacho signal from the fan is still needed on the inverter PCB.
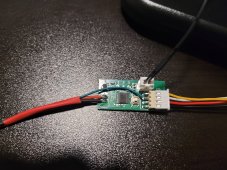
The left 3 wires are now connected to the inverter PCB fan connectors. The right 4 wires are connected via an adapter cable to the original fans (with the correct non-standard pinout). To feed the sense/tacho signal back to the inverter PCB I've just soldered the (left green wire) sense/tacho wire to the fan side sense/tacho wire (a bit ugly but it works). WIth this feedback, the inverter "see" the fan running and luckily it does not show error F01 (fan fault) and even with slow RPM (slower than the original RPM), the inverter does not complain.
For initial tests, I've programmed the temperature PWM controller to start with the slowest speed and start increasing the RPM starting at 35°C and reach maximum speed when 20°C more are reached (at 55°C). The controller increases the RPM in 19 steps between these two temperature ranges. It can be programmed as needed.
Now I need to do different tests to find out how much warmer the modded inverter will be compared to the original (at idle and different load and MPPT usage) to find the right settings.
For now, I have about 6-8°C higher temperature with the modded version when the inverter just idles at very low RPM.
The modded inverter is now VERY silent without load compared to the original without load!!!
I hope I will see also a lot of improvements even under different load scenarios.
In case I will see good test results over the coming weeks (I still not finished with my installation and can only test them without loads so far) and after fine tuned the temperature settings which are acceptable, I want to implement this change on all six inverters.
I will keep you updated.