Consumerbot3418
Fitting square pegs into round holes... for fun?
I picked up a B-stock second-hand Victron SmartShunt 500a, and recently integrated it into my split phase Multis. Since the Multis can only pump out 80a each (@14 volts=2240w). I wanted to install additional charging capacity, and be able to keep track of it. But now that I've completed the install, I'm surprised to see that the measured current (and power) at the shunt is substantially less than that reported by Multis--the current is off by up to 10%, and the power by 30%! In this chart, you can see the Multis charging with > 2500w, while the SmartShunt sees < 2000w.
I realize that there's a voltage drop across the DC bus, fuses, cables, and the shunt itself. That might (partially) account for the difference. But the large discrepancy in power had me concerned, questioning if bad crimps or connections may be to blame. Those 500w must be going somewhere, right?
So, at a steady 160 amps (as indicated by ve.bus/Multis, 155 amps on my clamp meter), I measured voltage drop from the battery bus bar to the inverter cables, and came up with a total of about 120mV, including fuses in the Lynx, main fuse, 2m of 4/0 cables, and lugs between. On my 12v system, that might account for about 20w lost to heat. Sure doesn't explain why 500w+ are missing!
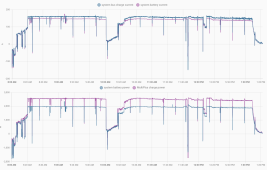
At this point, my best guess is that I have some combination of:
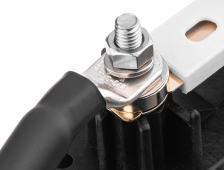
Sure doesn't look right to my (admittedly) non-expert eyes. I installed it with the lug contacting the fuse directly, and with one of the larger stainless washers between the spring washer and the lug. Anyone care to chime in with some advice?
Meanwhile, if the SmartShunt current reading is off by over 5% (but only at 100+ amps), is it possibly a faulty unit? Or are my expectations too lofty?

I realize that there's a voltage drop across the DC bus, fuses, cables, and the shunt itself. That might (partially) account for the difference. But the large discrepancy in power had me concerned, questioning if bad crimps or connections may be to blame. Those 500w must be going somewhere, right?
So, at a steady 160 amps (as indicated by ve.bus/Multis, 155 amps on my clamp meter), I measured voltage drop from the battery bus bar to the inverter cables, and came up with a total of about 120mV, including fuses in the Lynx, main fuse, 2m of 4/0 cables, and lugs between. On my 12v system, that might account for about 20w lost to heat. Sure doesn't explain why 500w+ are missing!
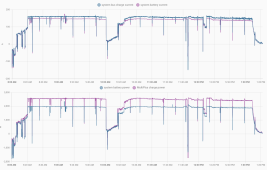
At this point, my best guess is that I have some combination of:
- Multis over-reporting charge current/power
- SmartShunt under-reporting current and voltage
- bad crimp(s)
- bad connection(s)
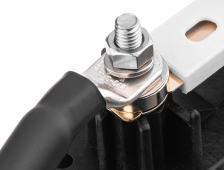
Sure doesn't look right to my (admittedly) non-expert eyes. I installed it with the lug contacting the fuse directly, and with one of the larger stainless washers between the spring washer and the lug. Anyone care to chime in with some advice?
Meanwhile, if the SmartShunt current reading is off by over 5% (but only at 100+ amps), is it possibly a faulty unit? Or are my expectations too lofty?
