Hey guys, it's time for the update:
the new BMS has arrived ... and now I'm even more confused than ever before ?
The BMS arrived today and I tried it out straight away, eager to finally get the project done. But when I connected it, the app still showed me the same undervoltage alarm, at the same cell even. I checked all the wires again, this time with a very accurate multimeter, and, measuring through the balancing leads, the voltage was pretty much exactly the same (±0,001V).
But the BMS App showed the Equi. Res. Alarm for cell #6 and measured it's voltage at roughly somewhere between 2.25V to 2.4V. The voltage it measured jumped around alot.
Although we already concluded last time that the balancing leads were okay, after switching them around on the plug and the cells, I tried out the new leads that were delivered with the new BMS.
Before I have tested it with the old ones, since I of course thought they were all good. (I still had them because the seller said it's okay if I keep the old balance leads, but I had to send back the BMS.)
So after about an hour of installing the new cables and making really sure everything is clean again, I tried again but to no avail.
The only difference was, that it now measures the voltage for cell #6 at around 2.7V to 2.8V (still jumping around)
Therefor I would normalls assume that there is indeed a bad contact at #6 somehow, but why would all my multimeters measure the cell correctly then? Is there perhaps a difference in how the BMS measures the voltage compared the to a multimeter?
I really have no idea what to try now, since I though buying a new BMS was already my last option and I was sure it would be successful ?
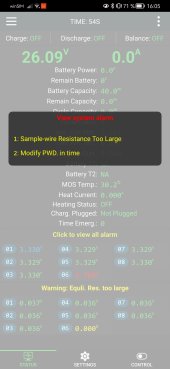
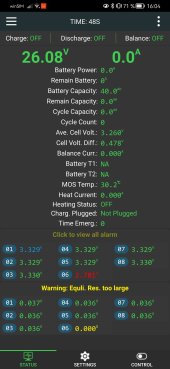
the new BMS has arrived ... and now I'm even more confused than ever before ?
The BMS arrived today and I tried it out straight away, eager to finally get the project done. But when I connected it, the app still showed me the same undervoltage alarm, at the same cell even. I checked all the wires again, this time with a very accurate multimeter, and, measuring through the balancing leads, the voltage was pretty much exactly the same (±0,001V).
But the BMS App showed the Equi. Res. Alarm for cell #6 and measured it's voltage at roughly somewhere between 2.25V to 2.4V. The voltage it measured jumped around alot.
Although we already concluded last time that the balancing leads were okay, after switching them around on the plug and the cells, I tried out the new leads that were delivered with the new BMS.
Before I have tested it with the old ones, since I of course thought they were all good. (I still had them because the seller said it's okay if I keep the old balance leads, but I had to send back the BMS.)
So after about an hour of installing the new cables and making really sure everything is clean again, I tried again but to no avail.
The only difference was, that it now measures the voltage for cell #6 at around 2.7V to 2.8V (still jumping around)
Therefor I would normalls assume that there is indeed a bad contact at #6 somehow, but why would all my multimeters measure the cell correctly then? Is there perhaps a difference in how the BMS measures the voltage compared the to a multimeter?
I really have no idea what to try now, since I though buying a new BMS was already my last option and I was sure it would be successful ?
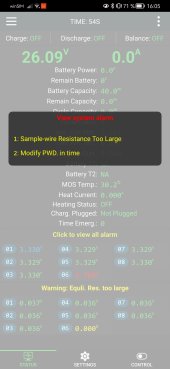
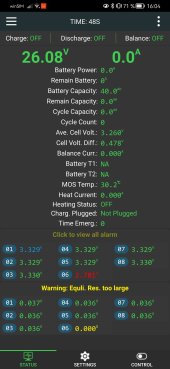