Frank in Thailand
making mistakes so you don't have to...
For a while now I have enough copper, but they are not usable for busbars.
Copper wire, AC tubing, small parts.
I got the crazy idea to make my own busbars by melting copper.
And make molds out of clay.
While the instructions look simple enough... It ain't.
First attempt:
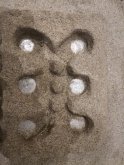
Looking good at start.
Problem with clay...
It shrinks.
Any measurements are off.
Next attempt was with wood.
Make wooden board of the correct size, and put clay around it.
Sounds great, as wood stay the same shape.
Sadly, wood can't be released from clay even when dry, so I heated it up, wood burns, yes?
Now it's more clear to me why ceramics slowly heat up their oven.
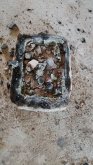
All small parts everywhere.
I made 2, the next one went little better.
but cracks
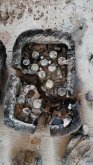
Only one looking good was the straight one.
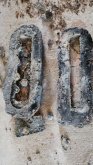
So I tried.
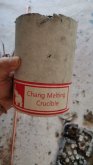
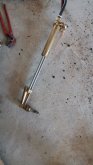
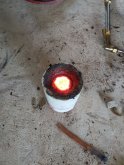
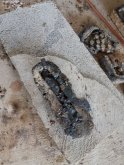
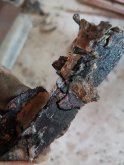
Apparently you can't make 2 pours in one mold.
It doesn't connect.
My 10 pictures are used, up to next part
Copper wire, AC tubing, small parts.
I got the crazy idea to make my own busbars by melting copper.
And make molds out of clay.
While the instructions look simple enough... It ain't.
First attempt:
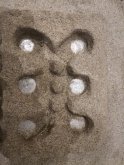
Looking good at start.
Problem with clay...
It shrinks.
Any measurements are off.
Next attempt was with wood.
Make wooden board of the correct size, and put clay around it.
Sounds great, as wood stay the same shape.
Sadly, wood can't be released from clay even when dry, so I heated it up, wood burns, yes?
Now it's more clear to me why ceramics slowly heat up their oven.
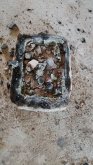
All small parts everywhere.
I made 2, the next one went little better.
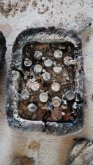
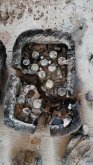
Only one looking good was the straight one.
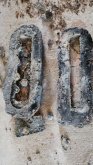
So I tried.
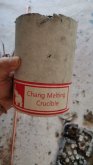
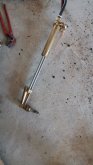
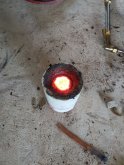
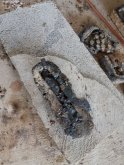
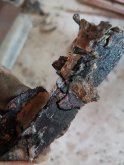
Apparently you can't make 2 pours in one mold.
It doesn't connect.
My 10 pictures are used, up to next part