Living hakuna
New Member
- Joined
- Nov 25, 2020
- Messages
- 14
Hello,
I'm getting 4 24V @170 batteries, connect then in series (48V) and parallel (340Ah).
The batteries from Bigbattery.com use an Andreson 175 connector so to get 3cables in 1 connector is impossible when using (1/0 gauge) cables so I want to know if this is ok to connect using POS/NEG bus bars. This will allow me to have two cables per connector.
Does this configuration look like I will achieve what I am looking for? Please ignore the charge controller from the bus bar it will go directly to the inverter.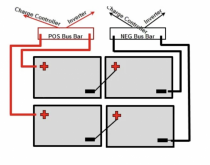
I'm getting 4 24V @170 batteries, connect then in series (48V) and parallel (340Ah).
The batteries from Bigbattery.com use an Andreson 175 connector so to get 3cables in 1 connector is impossible when using (1/0 gauge) cables so I want to know if this is ok to connect using POS/NEG bus bars. This will allow me to have two cables per connector.
Does this configuration look like I will achieve what I am looking for? Please ignore the charge controller from the bus bar it will go directly to the inverter.
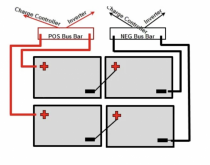