After 3 seasons my original SLA batteries on my RY48ZTR75 75 Ah pack started giving up the ghost. This thread, which I've been scanning for a while, has been invaluable in pulling off a replacement. After reading I decided on a couple of main factors in deciding on a replacement battery:
1. A full 48V unit to simplify replacement.
2. A battery with customer service backup I felt I could trust.
I couldn't find anything on Amazon that actually gave me a good feeling on #2. It's one thing returning and shipping back a pair of shoes. But on a battery that runs up to $1500 is a whole nother level.
I finally found a niche searching for 48V Lithium Golf Cart Batteries. I finally settled on this 48V 60 Ah Golf cart kit:
www.epochbatteries.com
I'm aware that I overpaid for the capacity I ended up getting. However, their distributor is in the local Atlanta area, so I was able to drive to the warehouse and pick up the kit. It was the only option I could find that met requirement #2 for me.
I had to do a bit of adjustment to get everything to fit. At 10.7 inches high, the battery modules were too tall to fit upright. I ended up turning both sideways with terminals facing the center of the tray. I also had to adjust the end brackets so they would fit with enough separation for the wiring.
I wired everything back except for the additional BAT+ connector that routes somewhere to the original charging port. It fired up on the first try.
It's interesting to see the combined BMS of the two units operate. Once the battery gets low there is a hard cutoff. Then after 45 seconds or so, the battery recovers, the BMS kicks back in, and the contactor on the lawn mower starts clicking. It'll then operate for a short amount of time before cycling. But I was able to drive it from the back yard back to the carport.
Getting the charger with the kit made charging simple. I just plugged it in and let it go. It cut off with a full charge on its own. I unplugged it anyway just in case.
I was able to cut an almost full 1 acre of tall tough grass before it cut off. And I'm pretty sure the batteries were not fully charged out of the box.
When I get a chance I'll follow up with pictures. Also I have to figure out how to integrate the meter that came with the kit to the mower. Also I know I'm going to need to add some spacers between and around the battery modules to ensure they stay in place on the tray.
But all in all I'd call this a successful replacement that only took a weekend to get done.
ga2500ev
1. A full 48V unit to simplify replacement.
2. A battery with customer service backup I felt I could trust.
I couldn't find anything on Amazon that actually gave me a good feeling on #2. It's one thing returning and shipping back a pair of shoes. But on a battery that runs up to $1500 is a whole nother level.
I finally found a niche searching for 48V Lithium Golf Cart Batteries. I finally settled on this 48V 60 Ah Golf cart kit:
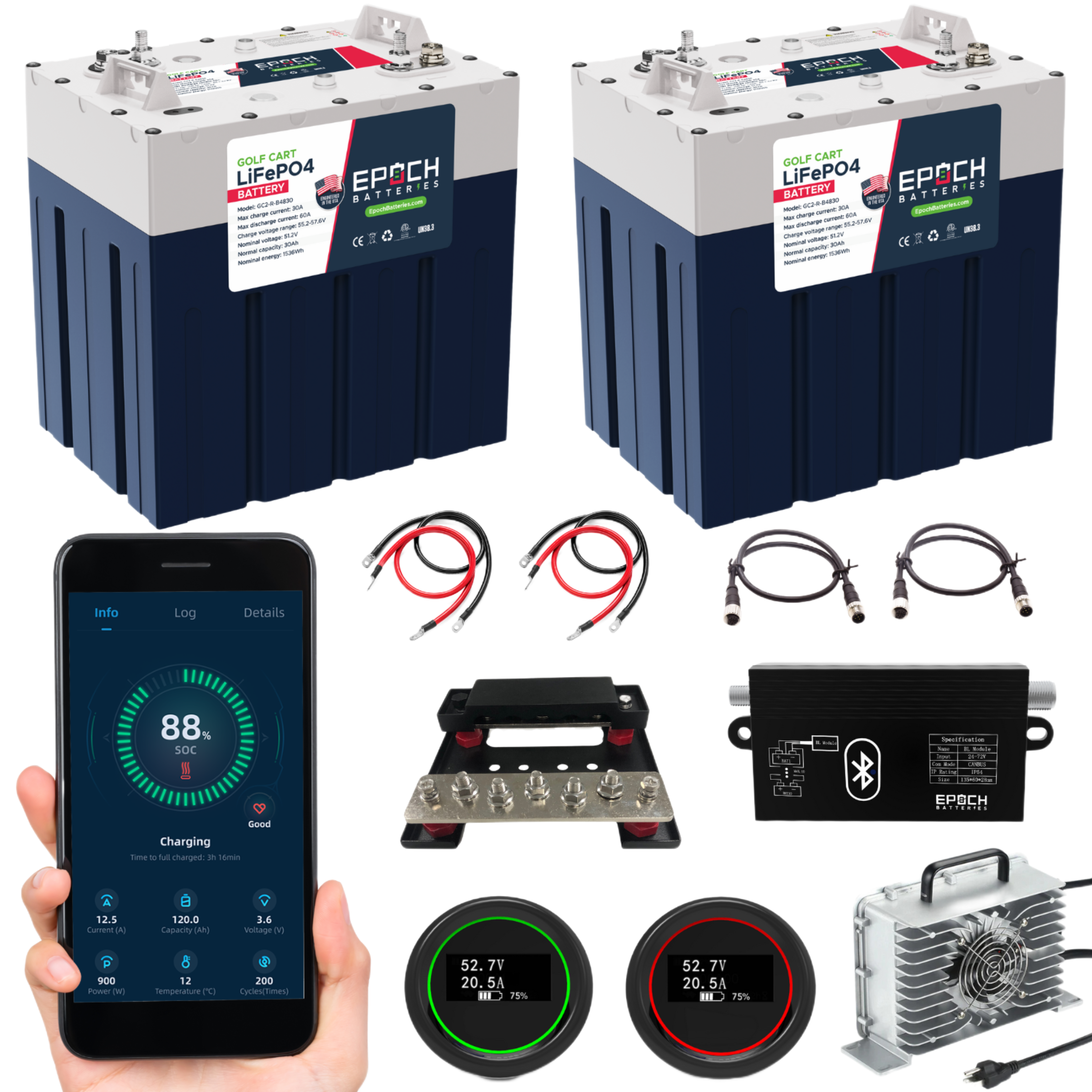
48V 60Ah GC2 Golf Cart LiFePO4 Lithium Battery Kit
Experience reliable and efficient performance with our 48V 60Ah GC2 LiFePO4 lithium battery kit. This complete kit includes a built-in BMS for protection and a fast 48V 22A charger. Enjoy up to 25 miles runtime and an 11-year warranty.
I'm aware that I overpaid for the capacity I ended up getting. However, their distributor is in the local Atlanta area, so I was able to drive to the warehouse and pick up the kit. It was the only option I could find that met requirement #2 for me.
I had to do a bit of adjustment to get everything to fit. At 10.7 inches high, the battery modules were too tall to fit upright. I ended up turning both sideways with terminals facing the center of the tray. I also had to adjust the end brackets so they would fit with enough separation for the wiring.
I wired everything back except for the additional BAT+ connector that routes somewhere to the original charging port. It fired up on the first try.
It's interesting to see the combined BMS of the two units operate. Once the battery gets low there is a hard cutoff. Then after 45 seconds or so, the battery recovers, the BMS kicks back in, and the contactor on the lawn mower starts clicking. It'll then operate for a short amount of time before cycling. But I was able to drive it from the back yard back to the carport.
Getting the charger with the kit made charging simple. I just plugged it in and let it go. It cut off with a full charge on its own. I unplugged it anyway just in case.
I was able to cut an almost full 1 acre of tall tough grass before it cut off. And I'm pretty sure the batteries were not fully charged out of the box.
When I get a chance I'll follow up with pictures. Also I have to figure out how to integrate the meter that came with the kit to the mower. Also I know I'm going to need to add some spacers between and around the battery modules to ensure they stay in place on the tray.
But all in all I'd call this a successful replacement that only took a weekend to get done.
ga2500ev