silverstone
Solar Enthusiast
- Joined
- May 3, 2022
- Messages
- 1,041
I FINALLY managed to put all cells inside my battery box and ... well ... a few things went wrong (again).
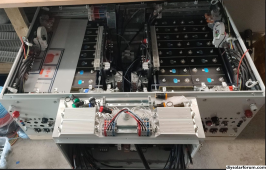
I'm kinda disappointed with the result really. The cost was quite high, the quality so-so and of course, for all the extra features I wanted such as contactor, light signaling, extra signal cables for feedbacks & 5V/24V PSU etc, there is NO PLACE TO PROPERLY ROUTE the cables. And every device on the side DIN rail cannot have anything "output" in the lower hole because it's in contact with the cells / cover. An absolute nightmare.
Might as well have bought a ready-to-go battery. Learned something along the way, but I think this was NOT the result I wanted
. Got the cost without the benefit really.
Now at least the cells are in and squeezed lightly. More than handtight (couldn't even turn the nut by hand, would have left 20mm of gap ! - yeah 20 mm !), but "tightened" I'd say reasonably, then backed off a few nut-turns (M10 - pitch is ... 1.75 mm ?). Sometimes you can pull out the yellow spacer and sometimes you cannot, that kinda tight. But cells are NOT too loose by any means. So they may have maybe 2-5 mm gap ACROSS 8 cells at around 50% SOC.
Now the question ... should I test every single of them ? They should be at around 50% SOC (3.26V - 3.29V) right now. With the EBC-A40L I can charge & discharge with 40A ... So theoretically that would be 280 Ah x (100% charge + 50% discharge) / 40 A = 10.5 hours / cell. Times 32 cells = 336 hours = 14 days full time ! More likely it's going to be 3 weeks. Not sure I'd like to wait that long to be honest
.
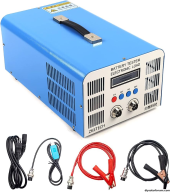
Cells were bought from Docanpower if that matters. They have been in long term storage for a while and no, unfortunately I didn't cycle them yet. Couldn't even move in my garage in the meantime.
Actually I discovered yesterday that ***** ... one cell from the second batch that I got delivered from Docanpower had suffered an electrolyte leakage probably during transport (I only noticed it now several months later when I *could* open the packages).
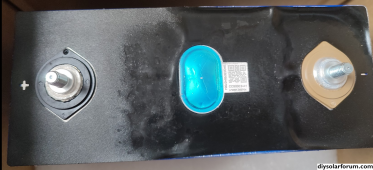
I promply contacted Docanpower about it. Let's see how they react.
Thankfully I had one cell as spare and put that in instead, even though it was from the first batch, so a bit older ....
By the way, how do you evaluate the status of the pressure relief vent/seal?
Some look "clean & tidy" (just the gold dot in the middle with the 3 weak spots the blow over pressure), some have "slight" bleeding (black color) around the middle gold dot, .... They are all different
.
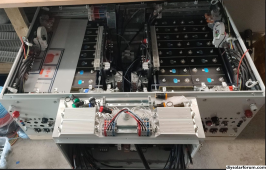
I'm kinda disappointed with the result really. The cost was quite high, the quality so-so and of course, for all the extra features I wanted such as contactor, light signaling, extra signal cables for feedbacks & 5V/24V PSU etc, there is NO PLACE TO PROPERLY ROUTE the cables. And every device on the side DIN rail cannot have anything "output" in the lower hole because it's in contact with the cells / cover. An absolute nightmare.
Might as well have bought a ready-to-go battery. Learned something along the way, but I think this was NOT the result I wanted
Now at least the cells are in and squeezed lightly. More than handtight (couldn't even turn the nut by hand, would have left 20mm of gap ! - yeah 20 mm !), but "tightened" I'd say reasonably, then backed off a few nut-turns (M10 - pitch is ... 1.75 mm ?). Sometimes you can pull out the yellow spacer and sometimes you cannot, that kinda tight. But cells are NOT too loose by any means. So they may have maybe 2-5 mm gap ACROSS 8 cells at around 50% SOC.
Now the question ... should I test every single of them ? They should be at around 50% SOC (3.26V - 3.29V) right now. With the EBC-A40L I can charge & discharge with 40A ... So theoretically that would be 280 Ah x (100% charge + 50% discharge) / 40 A = 10.5 hours / cell. Times 32 cells = 336 hours = 14 days full time ! More likely it's going to be 3 weeks. Not sure I'd like to wait that long to be honest
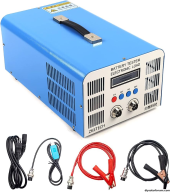
Cells were bought from Docanpower if that matters. They have been in long term storage for a while and no, unfortunately I didn't cycle them yet. Couldn't even move in my garage in the meantime.
Actually I discovered yesterday that ***** ... one cell from the second batch that I got delivered from Docanpower had suffered an electrolyte leakage probably during transport (I only noticed it now several months later when I *could* open the packages).
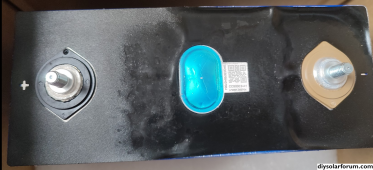
I promply contacted Docanpower about it. Let's see how they react.
Thankfully I had one cell as spare and put that in instead, even though it was from the first batch, so a bit older ....
By the way, how do you evaluate the status of the pressure relief vent/seal?
Some look "clean & tidy" (just the gold dot in the middle with the 3 weak spots the blow over pressure), some have "slight" bleeding (black color) around the middle gold dot, .... They are all different
Last edited: