Aridom82
Learning addict
I am building a kiln with sic heating elements, and i am going to power with my inverters. The power will be controlled through pwn duty cycle.
Considering that the inverter is pretty complicated and has to respond in real time to the power demand using different sources, could this switching on and off duty cycle way of controlling the power output potentially damage the inverter? What frequency of the square wave would you use? Could a capacitor big enough help somewhere to smooth it?
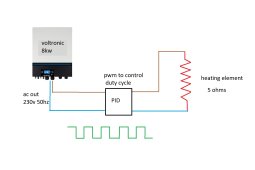
Considering that the inverter is pretty complicated and has to respond in real time to the power demand using different sources, could this switching on and off duty cycle way of controlling the power output potentially damage the inverter? What frequency of the square wave would you use? Could a capacitor big enough help somewhere to smooth it?
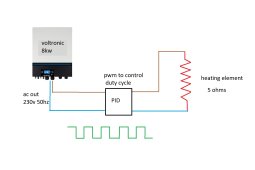