Steve_S
Offgrid Cabineer, N.E. Ontario, Canada
Good Day Folks,
I am posting this in ADVANCE as I have been fielding questions in PM and figured I should share what's happening and answer the Q's for everyone, so I thought a small information update is due for the membership here. When the New Manuals etc are posted, I will update the resource section.
Jason has been listening & hearing the input from the BMS users and so things have changed up a bit as a result.
- New 4.1 Owner's Manuals will be out after some corrections this week (I hope). [Just looking at the new drafts now]
- Firmware updates have been done and will be posted as well. (if not already)
- New Shunts have been tested & selected which will now be available.
- New DCC Contactors have been developed by & for Chargery which have some great features that were very needed. sorry I don't know what the pricing will be.
I hope to be able to test the new DCC Contactors soon but it is outside of my hands at this time.
The new Shunts :
The new DCC Contactors:
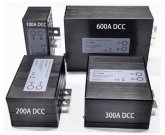
The new DCC-300 showing Big Lug useability.
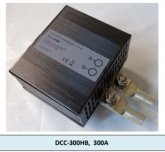
For the Really Curious !
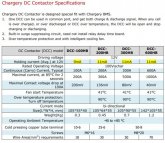
I am posting this in ADVANCE as I have been fielding questions in PM and figured I should share what's happening and answer the Q's for everyone, so I thought a small information update is due for the membership here. When the New Manuals etc are posted, I will update the resource section.
Jason has been listening & hearing the input from the BMS users and so things have changed up a bit as a result.
- New 4.1 Owner's Manuals will be out after some corrections this week (I hope). [Just looking at the new drafts now]
- Firmware updates have been done and will be posted as well. (if not already)
- New Shunts have been tested & selected which will now be available.
- New DCC Contactors have been developed by & for Chargery which have some great features that were very needed. sorry I don't know what the pricing will be.
I hope to be able to test the new DCC Contactors soon but it is outside of my hands at this time.
The new Shunts :
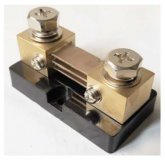
The new DCC Contactors:
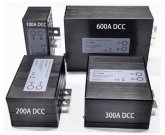
The new DCC-300 showing Big Lug useability.
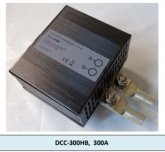
For the Really Curious !
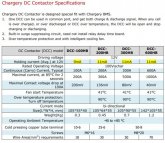