thegoogler
New Member
- Joined
- Apr 15, 2021
- Messages
- 108
Thanks, that's good info.This question is much discussed in many threads around this forum. Msny users here do choose thread locker. After trying both, and finding that epoxy is much stronger, that’s just what I chose. Many have found that LokTite does not bond well to the aluminum without using an “accelerant“.
It is very important to use one, or the other. These aluminum terminals a very soft, and the threads are shallow. It is scary to feel one of your studs pulling out as you gently tighten a nut. I was able to salvage that terminal by fixing the stud with epoxy. That was what tipped me to now using epoxy with the very first install of every stud.
it is certainly possible to repair a damaged terminal thread with a heli-coil insert. But I have 48 cells (96 terminals) in service, and I don’t want to mess with a bunch of heli-coil repairs if I can avoid it easily and cheaply with the epoxy.
My big concern with helicoils is they are stainless steel being mounted into aluminum, which risks galvanic corrosion over time. I would not use anything in aluminum other than zinc. YMMV of course.
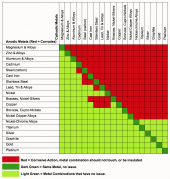