Old_Skewler
Solar Enthusiast
This is for an off-grid 15 KWh 48V battery bank (3x EG4s) connected to a Schneider 4048 Inverter in split-phase. The system has been running well for over a year. I would like to get feedback on how you'd deal with these warnings if you were running this system. I have a total of (3) alarm and warnings:
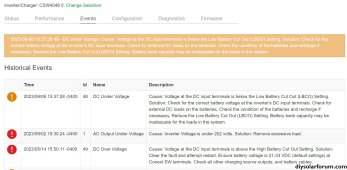
Here is the battery BMS information as read by the inverter. The most recent event happened when battery around 50% and 48V. Very small load on system, less than 200W.
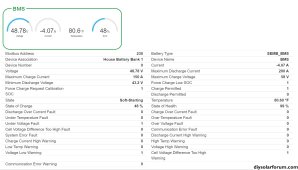
And here is the battery setting screen with a 47V LBCO:
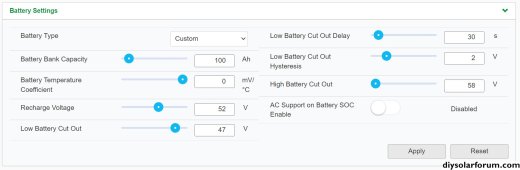
1. DC Under Voltage: i suspect the LBCO setting is too high and needs to be lowered? I don't remember where I got this 47V setting from (@SignatureSolarTech or Schneider).
2. AC Output Under Voltage: is there a way in InsightHome to access historical data and verify the AC load at the moment this event happened? Anything else I should be looking into regarding this event?
3. DC Over Voltage: this must've been the Inverter when in charging mode. I currently have the following charger settings.
Bulk/Boost Voltage Set Point: 57.6V
Bulk Termination Voltage: 56.8V
Absorption Voltage Set Point: 56.8V
I am not sure whether i should be looking into updating the charging numbers above OR increasing the HBCO. Any thoughts?
Thanks in advance for any feedback!
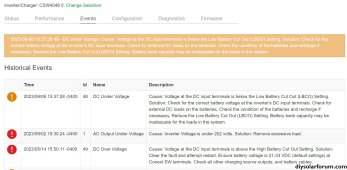
Here is the battery BMS information as read by the inverter. The most recent event happened when battery around 50% and 48V. Very small load on system, less than 200W.
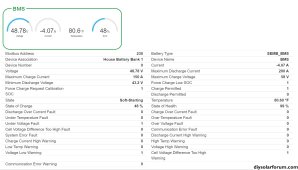
And here is the battery setting screen with a 47V LBCO:
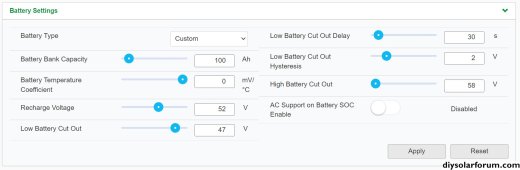
1. DC Under Voltage: i suspect the LBCO setting is too high and needs to be lowered? I don't remember where I got this 47V setting from (@SignatureSolarTech or Schneider).
2. AC Output Under Voltage: is there a way in InsightHome to access historical data and verify the AC load at the moment this event happened? Anything else I should be looking into regarding this event?
3. DC Over Voltage: this must've been the Inverter when in charging mode. I currently have the following charger settings.
Bulk/Boost Voltage Set Point: 57.6V
Bulk Termination Voltage: 56.8V
Absorption Voltage Set Point: 56.8V
I am not sure whether i should be looking into updating the charging numbers above OR increasing the HBCO. Any thoughts?
Thanks in advance for any feedback!