I have just finished setting up a system with:
14 455w panels in two strings
42kw LG NMC batteries in 6.5kw modules
Growatt 12000T MPV
I have param 1 set to SBU. So I should see the PV array being used for house load during the day, with batteries coming in only if load > available PV current.
What I see instead is the PV being used for house load and battery charging in the morning, and then when the batteries are topped off the PV array is no longer utilized and batteries are exclusively used to power house load.
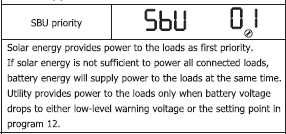
Any ideas?
Acceptable input range for the MPP controller is 60–245 V.
PV voltages and currents:

14 455w panels in two strings
42kw LG NMC batteries in 6.5kw modules
Growatt 12000T MPV
I have param 1 set to SBU. So I should see the PV array being used for house load during the day, with batteries coming in only if load > available PV current.
What I see instead is the PV being used for house load and battery charging in the morning, and then when the batteries are topped off the PV array is no longer utilized and batteries are exclusively used to power house load.
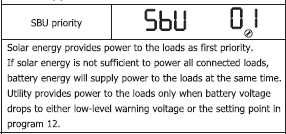
Any ideas?
Acceptable input range for the MPP controller is 60–245 V.
PV voltages and currents:

Attachments
Last edited: