Odd one for you all. Short version, no battery percentage or AH info and logs are too small. Bonus, maybe 1 bad cell.
I went to bed at 1030, battery was 60-70%, at around 3am the hot water element came on (1800w) on a schedule. I've run this before for a few hours at a time, but usually when the battery is in the top end (dumping excess solar into hot water) without any issues.
It ran for 10mins and then the inverter switched off (can see off time from MPP inverter logs) I assume because the BMS disconnected the battery. Now as the MPP has tried to restart, the BMS sees that as a short so it's filled the logs with short circuit protection errors until I've gotten up and plugged in a power supply on the output side of the BMS to give the inverter a chance to charge its caps and everything was back up and running. But logs don't go far enough back for me to tell what happened. I immediately tested the hot water element again, ran it for 20mins, had no issues then switched it off.
Since then, there's no capacity or AH info in the BMS screen, see screen shot.
Do I need to fully reboot the BMS? It's been up for over 40 days. If I do need to reboot it, what's the process as I've heard horror stories about disconnecting/reconnecting the wrong ends at the wrong time.
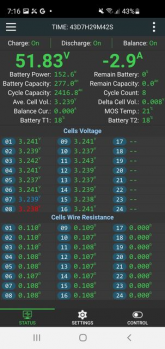
As for why it switched off, I think cell 14 might be an issue, as per my other thread it's hitting HVD well before others, I thought maybe it was not balanced and have switched on balancing sooner (but the pack was paralleled for almost 2wks before commissioning), but now I am seeing it is also dropping much further under load. In these 2 screen shots You can see it dipping well below pack average voltage and then in the next image, being close to the others (but I think it's because in the image where it's not as far below, the balance current is positive and likely going into that cell).
I have started chatting with Ali about the cell.
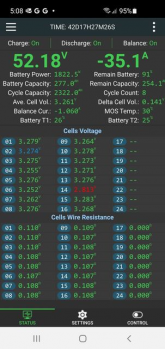
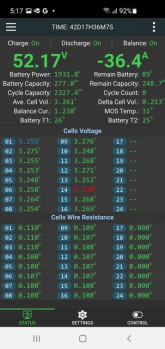
Since restarting the inverter I also see this Eeprom fault but logs do not go far enough back for me to tell if that was there last time I switched the inverter on. Ignore the line in fault, that was me turning AC input off.
I have ordered a USB/RS485 setup so I can put a PC in there and log properly from the watch power app for the inverter and maybe Grafan for the BMS.
All help appreciated
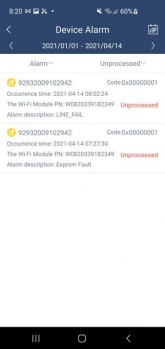
I went to bed at 1030, battery was 60-70%, at around 3am the hot water element came on (1800w) on a schedule. I've run this before for a few hours at a time, but usually when the battery is in the top end (dumping excess solar into hot water) without any issues.
It ran for 10mins and then the inverter switched off (can see off time from MPP inverter logs) I assume because the BMS disconnected the battery. Now as the MPP has tried to restart, the BMS sees that as a short so it's filled the logs with short circuit protection errors until I've gotten up and plugged in a power supply on the output side of the BMS to give the inverter a chance to charge its caps and everything was back up and running. But logs don't go far enough back for me to tell what happened. I immediately tested the hot water element again, ran it for 20mins, had no issues then switched it off.
Since then, there's no capacity or AH info in the BMS screen, see screen shot.
Do I need to fully reboot the BMS? It's been up for over 40 days. If I do need to reboot it, what's the process as I've heard horror stories about disconnecting/reconnecting the wrong ends at the wrong time.
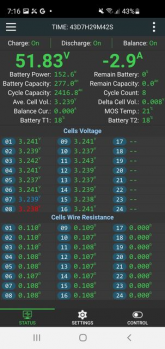
As for why it switched off, I think cell 14 might be an issue, as per my other thread it's hitting HVD well before others, I thought maybe it was not balanced and have switched on balancing sooner (but the pack was paralleled for almost 2wks before commissioning), but now I am seeing it is also dropping much further under load. In these 2 screen shots You can see it dipping well below pack average voltage and then in the next image, being close to the others (but I think it's because in the image where it's not as far below, the balance current is positive and likely going into that cell).
I have started chatting with Ali about the cell.
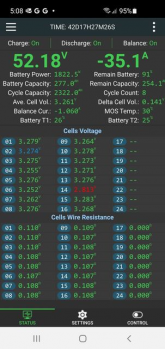
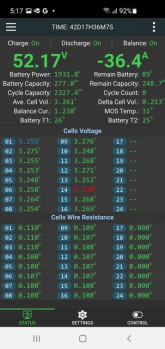
Since restarting the inverter I also see this Eeprom fault but logs do not go far enough back for me to tell if that was there last time I switched the inverter on. Ignore the line in fault, that was me turning AC input off.
I have ordered a USB/RS485 setup so I can put a PC in there and log properly from the watch power app for the inverter and maybe Grafan for the BMS.
All help appreciated
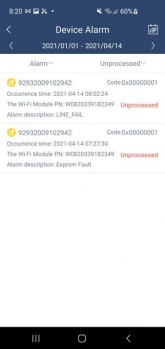
Last edited: