Ron-ski
Solar Enthusiast
I'm building my own 48v battery rack, capable of holding 4 batteries consisting of 16 EVE 280ah cells each. To start with I'll only have one battery, I will probably add another once funds allow. Electrician will be doing the AC side, and I'm dealing with the DC side.
Equipment list so far for the battery/inverter side of things:
Cable run from the battery to the Lynx Power in would be about 3.2m (bottom shelf), and I was looking at using 70mm cable, something like this.
I don't 100% trust the DC breakers so would also like a fuse close to the battery positive which I understand has to be a T class, but not sure on what the rating should be?
Also not sure if I've got the correct rated DC circuit breakers, 160A was intended for individual batteries, 250A to turn off/protect the whole rack (not needed with Lynx system)?
Should I also fuse the Lynx Power in? If so what fuses?
The inverter is rated at constant of 8000w, but a peak of 16000w, although I doubt we'll draw that much, so this confuses me somewhat as what the fuses should be used should there be a large peak.
Also how critical is it that all the battery cables are the same length?
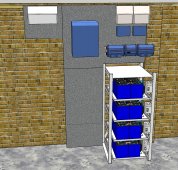
Equipment list so far for the battery/inverter side of things:
- Victron Quattro 48/10000 (will be grid tied)
- 275A isolator switch for inverter
- Lynx Power In (can be fused)
- Lynx Smart Shunt 1000
- Lynx Distributor
- JK BMS 200A (B2A20S20P-CAN)
- 250A two pole DC circuit breaker/switch
- 160A two pole DC circuit breaker/switch
- 16 Eve 280Ah cells
Cable run from the battery to the Lynx Power in would be about 3.2m (bottom shelf), and I was looking at using 70mm cable, something like this.
I don't 100% trust the DC breakers so would also like a fuse close to the battery positive which I understand has to be a T class, but not sure on what the rating should be?
Also not sure if I've got the correct rated DC circuit breakers, 160A was intended for individual batteries, 250A to turn off/protect the whole rack (not needed with Lynx system)?
Should I also fuse the Lynx Power in? If so what fuses?
The inverter is rated at constant of 8000w, but a peak of 16000w, although I doubt we'll draw that much, so this confuses me somewhat as what the fuses should be used should there be a large peak.
Also how critical is it that all the battery cables are the same length?
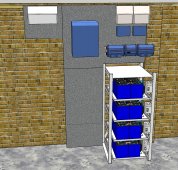
Last edited: