I spent the day at the storage lot yesterday and made good progress. The new step drill bits did a nice job. A quick swipe with sandpaper cleaned up the contact area nicely.
I hauled my drill press and chop saw to the storage lot and that worked out really well, but that drill press is really heavy even though it's a benchtop model.
In the picture below, anything that is bright copper is new, the common bus bars (big shiny things) are also new. None of the devices are secured down, covers aren't on and the cable strain relief isn't in place yet either. All this in in preparation of wiring up my new inverter which calls for two cables on each DC leg (pos/neg), four total. I think this new setup is going to be more efficient. I have been stacking cable lugs on posts and I have to wonder if my batteries weren't as well balanced as they could be for charge and discharge. I'm referring mainly to the lugs on the shunt and the Class T fuse.
Some adjustments still need to be made. It's a little rough. I was out of time. It was dark, my flashlight batteries needed a charge and it was 35° F.
I am not impressed with the dinky little M6 studs on the Victron Battery Protect 65.
@noenegdod, the lowest speed on my drill press is 850 rpm. That's higher than I thought.
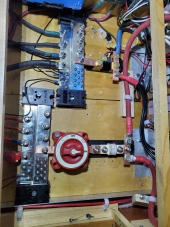
I hauled my drill press and chop saw to the storage lot and that worked out really well, but that drill press is really heavy even though it's a benchtop model.
In the picture below, anything that is bright copper is new, the common bus bars (big shiny things) are also new. None of the devices are secured down, covers aren't on and the cable strain relief isn't in place yet either. All this in in preparation of wiring up my new inverter which calls for two cables on each DC leg (pos/neg), four total. I think this new setup is going to be more efficient. I have been stacking cable lugs on posts and I have to wonder if my batteries weren't as well balanced as they could be for charge and discharge. I'm referring mainly to the lugs on the shunt and the Class T fuse.
Some adjustments still need to be made. It's a little rough. I was out of time. It was dark, my flashlight batteries needed a charge and it was 35° F.
I am not impressed with the dinky little M6 studs on the Victron Battery Protect 65.
@noenegdod, the lowest speed on my drill press is 850 rpm. That's higher than I thought.
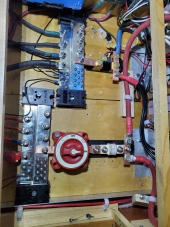