I'm expanding this discussion to include EVE two-hole terminal contact options. I'm not excited by the limited surface area of the two-hole post as displayed on e.g. 18650batterystore for the LF230:
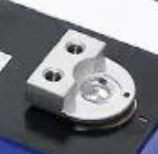
That seems fine if you're going to use two-hole solid busbars across the full length of the terminal, in which case you use the full (albeit somewhat minimal) surface area.
But what if you don't want to use solid busbars because you know the cells are going to expand and contract with high current I/O and age, and you can't find suitable two-hole flexible busbars? eelbattery does make a single hole flexible version with 54mm spacing that would suite the single stud LF230, but maybe not the two-hole terminal.
I'm currently thinking that I'll just make my own series connections with 1/0 cable that I have left over, with quality tinned copper lugs (Ancor), and use 316 stainless steel grub screws for the best corrosion resistance I can work out in these aluminum terminals. I'm also considering aluminum threaded rod and aluminum serrated flange nut to achieve good contact from above, too. And there's copper braid.
I'm skeptical that the lug on a single SS stud on this abbreviated terminal surface will achieve adequate surface contact for 1C draw.
And so I'm starting to consider two-hole telecom lugs such as

(but I really would want one that does a right turn and haven't found that yet), or a segment of tinned copper bar stock cut and drilled to adapt full connection to the two-hole terminal, to e.g. a 5/16 bolt hole for single lug connection that would maximize contact.
Am I overthinking this? Would a single Ancor 1/0 x 1/4-in lug angled off the inner corner of this terminal afford adequate contact for 1C draw from e.g. an EVE LF230 cell? I suppose I could connect it to the "far" terminal--the one furthest from the cable exit direction, so the lug crosses towards the second hole. Now that I think further, maybe that's adequate contact area? This is just for a 4S 12V string, max draw expected maybe 160A, infrequently. I think I'm overthinking it...
I've seen mention of antioxidant paste, but I've read that there are different pastes for aluminum and for copper, and one should not be used with the other. What paste, if any, would be appropriate for a tinned copper and aluminum connection?