dougbert
Solar Addict
A little change of plans for me.
First I do my taxes and am getting a refund that can help me buy 2 more batteries, and then this happened.
My Trace SW4024 inverter has an internal fan and I was startled with a very loud rattle sound coming from the inverter and determined that the FAN was wobbling and making the noise. I knew the fans fail and this one is 21 years old so after much searching I believe I found a replacement and ordered it for $30. During that search I came across an ebay ad for a Xantrex/Trace SW Plus 5548 inverter for sale. After ordering the fan and revisited the 5548 ad, read what was posted and looked at the beautiful pictures of clean inverter
I then searched and searched and found the operations manual for the unit. I looked up the programming characteristics for this unit and they were similar to my existing inverter's ability. Namely, the support voltages down to 32v while my current unit supports down to 36 volts. And the top charging voltage fits fine, just like my existing unit. So the Tesla charging parameters are fully supported by this 5548 inverter. Sweet!
This inverter supports 5500 watts of load and the better part is, it is a 48volt battery based inverter. I can re-arrange my 6 batteries into 48 volt configuration and swap out my old inverter with the new (to me - it was made in Mar 2005, while my old came from 1999 time frame).
It still is only 120vac for loads, but I can live with that for now.
So I bought it and should get here Feb 17th. Patting myself on the back at the moment, hoping I did right.
here is the seller's remarks:
Xantrex/Trace SW Plus 5548 Charger Inverter. Condition is "Used".
This is a Xantrex SW Plus Inverter with 5500 watts and 48 volts of battery in perfect working condition and looks like new.
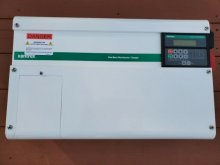
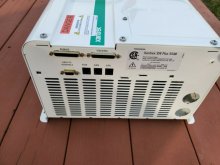
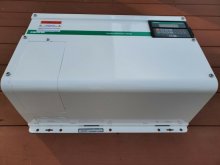
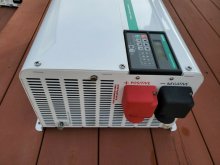
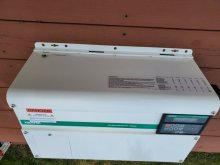
First I do my taxes and am getting a refund that can help me buy 2 more batteries, and then this happened.
My Trace SW4024 inverter has an internal fan and I was startled with a very loud rattle sound coming from the inverter and determined that the FAN was wobbling and making the noise. I knew the fans fail and this one is 21 years old so after much searching I believe I found a replacement and ordered it for $30. During that search I came across an ebay ad for a Xantrex/Trace SW Plus 5548 inverter for sale. After ordering the fan and revisited the 5548 ad, read what was posted and looked at the beautiful pictures of clean inverter
I then searched and searched and found the operations manual for the unit. I looked up the programming characteristics for this unit and they were similar to my existing inverter's ability. Namely, the support voltages down to 32v while my current unit supports down to 36 volts. And the top charging voltage fits fine, just like my existing unit. So the Tesla charging parameters are fully supported by this 5548 inverter. Sweet!
This inverter supports 5500 watts of load and the better part is, it is a 48volt battery based inverter. I can re-arrange my 6 batteries into 48 volt configuration and swap out my old inverter with the new (to me - it was made in Mar 2005, while my old came from 1999 time frame).
It still is only 120vac for loads, but I can live with that for now.
So I bought it and should get here Feb 17th. Patting myself on the back at the moment, hoping I did right.
here is the seller's remarks:
Xantrex/Trace SW Plus 5548 Charger Inverter. Condition is "Used".
This is a Xantrex SW Plus Inverter with 5500 watts and 48 volts of battery in perfect working condition and looks like new.
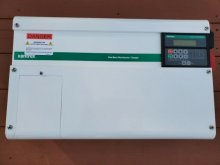
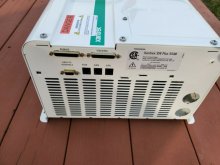
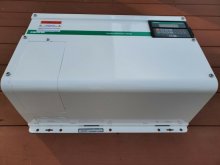
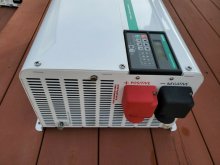
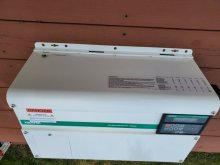
Last edited: