St0fzuiger
New Member
- Joined
- Aug 30, 2020
- Messages
- 7
Hello all,
Not really Solar related but mainly on the Daly BMS as i found the most info here.
I have the Daly 30/60A Smart BMS with the Bluetooth adapter and use the newer app "Smart BMS" from Daly.
Now i want to change some parameters but it requests an 6 number password.
I searched like crazy but found nothing.
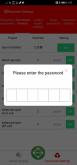
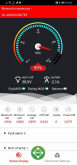
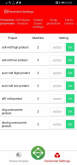
I hope anyone here has an idea since the response from Daly is crazy slow
Thanks!
Not really Solar related but mainly on the Daly BMS as i found the most info here.
I have the Daly 30/60A Smart BMS with the Bluetooth adapter and use the newer app "Smart BMS" from Daly.
Now i want to change some parameters but it requests an 6 number password.
I searched like crazy but found nothing.
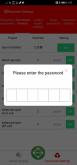
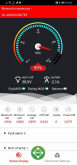
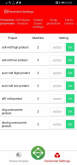
I hope anyone here has an idea since the response from Daly is crazy slow
Thanks!